RotoMoulding 2.0
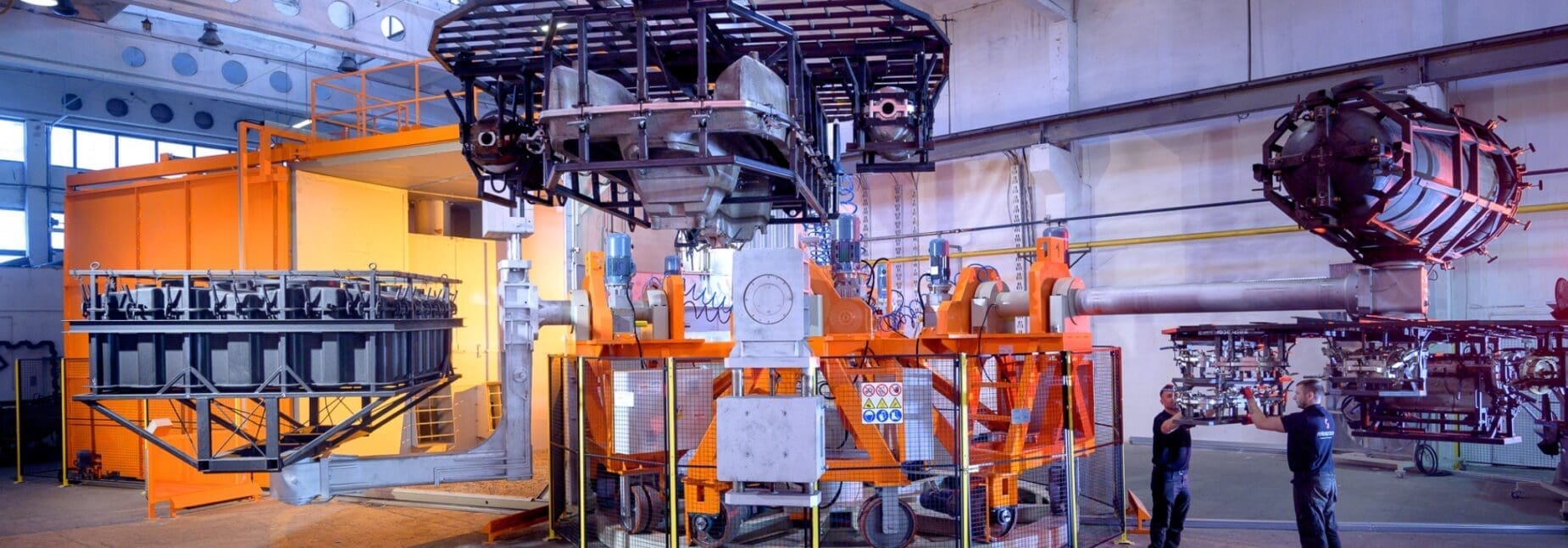
RotoMoulding 2.0 is not only the next stage in the development of rotational plastic moulding technology. Because this approach goes deeper. It is based on the use of unique knowledge from over twenty years’ worth of experience of specialists and on developed original standards and procedures. And these enable us to undertake even the most demanding tasks, thus providing Clients with solutions for projects with the highest level of complexity while maintaining the highest quality of their execution.
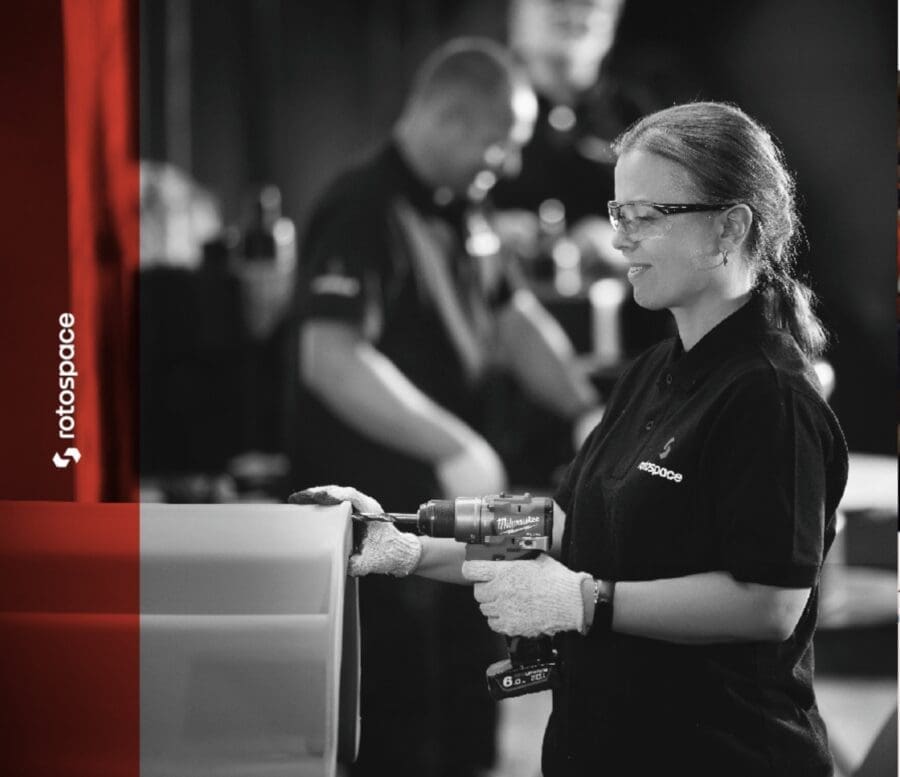
According to RotoMoulding 2.0, each product which leaves the company should not only be functional, but also compliant with the highest quality standards which the Client expects from us, but also those which we require from ourselves. TechStandard™ is the guarantee of fulfilling the promise of delivering a high-quality product as it ensures:
- dimensional accuracy by applying the strictest tolerance standards within the range of +/- 1%,
- guarantee of a reliable appearance and a perfectly smooth surface (SilkTest™),
- perfectly seated inserts
- resistance to weather co
- simple, large surfaces and long lines which meet the highest aesthetic and functional standards,
- repeatable, identical products, and elimination of their variability,
- possibility of manufacturing products with a diameter of up to 4.5 metres
RotoMoulding 2.0 takes care of the natural environment. We are aware of the impact of the industry on the environment, therefore, in accordance with the original CarbonFootprint Control™ standard, we strive to minimize consumption of raw materials and reduce waste by optimizing production processes and using environmentally friendly materials.
What is more, RotoMoulding 2.0 concerns not only the manufacturing stage, but also the post-manufacturing one. Complex and ambitious productions and product quality depend on the condition of the mould. Therefore, it requires special care, maintenance, and storage between production seasons. In RotoMoulding 2.0, the orignal MouldProtection™ Programme stands for a set of designed and implemented procedures for storing and protecting entrusted moulds.
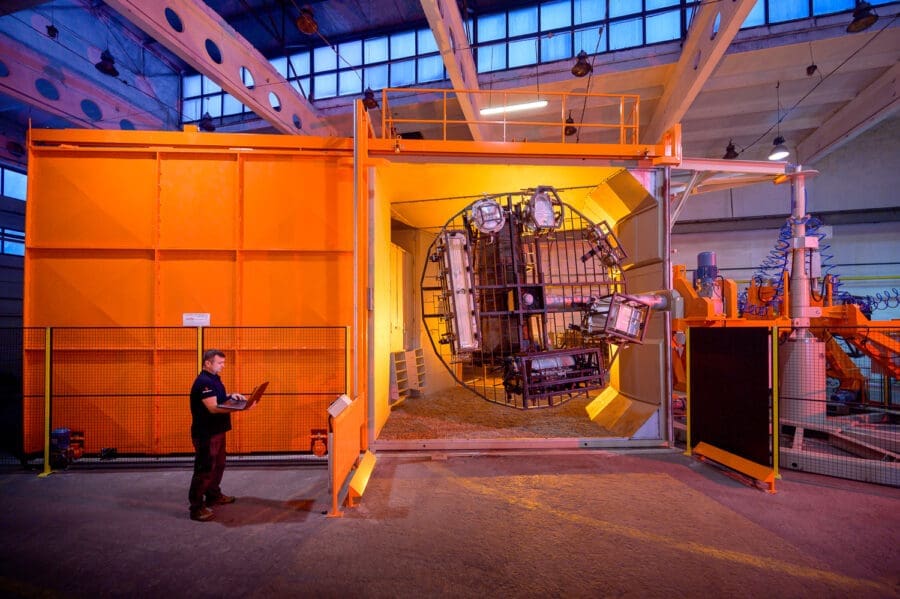
All this together creates a standard that is tantamount to reliability, precision and an innovative approach to component manufacturing.
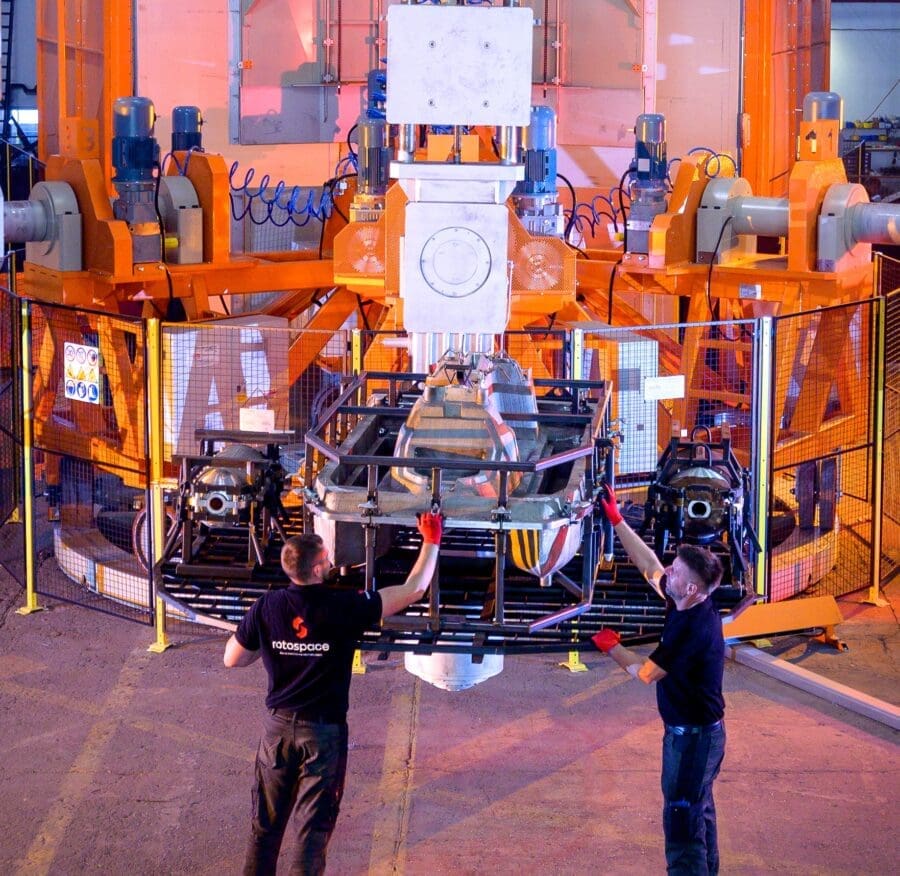