Rotomoulding2.0
In RotoMoulding 2.0, the most important thing is to implement ambitious projects. What other companies may find impossible, we see as an inspiring challenge. Throughout the entire rotary machining process, we strive to redefine boundaries, set new quality standards and production possibilities.
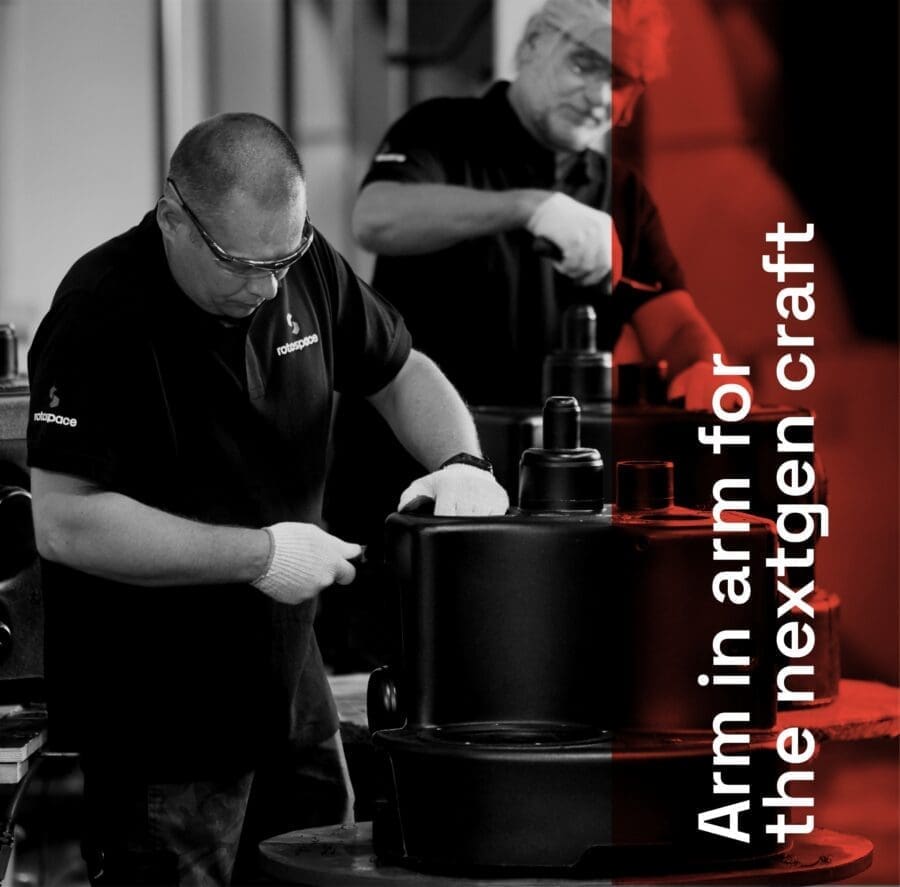
Rotospace to firma powstała w Międzyrzeczu – mieście będącym kolebką rotomouldingu.
Jesteśmy liderem w produkcji wysokiej jakości komponentów dzięki innowacyjnej filozofii wpływającej na Rotoformowanie. Nasze 20 letnie doświadczenie w branży rotational moulding oraz zaawansowane technologie produkcji pozwalają nam dostarczać produkty najwyższej jakości. Rotospace łączą tradycja i produkcja z nowoczesnym podejściem do rotoformowania, zapewniając precyzję, niezawodność i efektywność w każdym detalu. Nasza oferta obejmuje szeroki zakres produktów technologii Rotomoulding oraz obsługę na każdym etapie produkcji. Nasze produkty są rezultatem zaawansowanych procesów produkcji, gdzie każdy element ma znaczenie. Odkryj możliwości, jakie oferuje Rorotomoulding 2.0
Why Us
RotoMoulding 2.0
An original philosophy of approach to implementation of ambitious projects, base...
Find out more
TechStandard™
Guarantees fulfillment of the promise of delivering a high-quality product throu...
Find out more
SilkTest™
Guarantees a reliable appearance and a perfectly finished surface. All surfaces ...
Find out more
MouldProtection™Program
A comprehensive set of designed and implemented procedures which ensures protect...
Find out more
Custom PreHeating™
Achieving the best results by means of appropriate heating prior to the forming ...
Find out more
PreOrder Standard™
A manufacturing and inventory management method which allows for quicker deliver...
Find out more
CarbonFootprint Control™
An original standard for counting and controlling the generated carbon footprint...
Find out more
Doświadczenie
For over 20 years, our specialists have been creating the rotomoulding industry ...
Find out more